
Every Industry is under growing pressure to limit its environmental impact and improve performance and sustainability.
Reducing negative impact on the environment presents savings for business and future generations. The easiest way to decrease impact on the environment around us when using compressed air is to make sure that your system and equipment is running as effectively as possible. An efficient system will help reduce energy costs and in turn cut carbon emissions.
Why I should bother about climate change?
Because, The Earth’s atmosphere is warming, faster than ever. Global temperatures have been rising for well over a century, accelerating in recent years, and are now the highest on record. The severe implications of these changes in climate are recent floods in Pakistan, Fire in Amazon, melting of Antarctic Glacier and posing threat of in crease of sea level by several feet.
The reason? Carbon (CO2) emissions are causing the greenhouse effect, trapping heat, and making our world warmer, faster than could ever happen naturally. Reducing carbon pollution is essential if we are to keep our planet’s temperature in check.
What me and my company can do?
Following are some steps you can take to reach a win-win situation where you will be saving electricity bill whilst earning carbon credits.
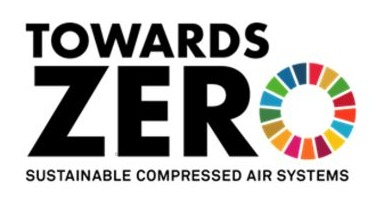
Monitor Compressed Air Energy Use?
If you can’t measure it, you can’t improve it!
It is important to monitor how much energy your system is using. By tracking energy usage you can quickly identify if you are wasting energy.
Carrying out an energy audit is an ideal way to start this process and identify areas where you can make improvements
Check for Air Leaks
Leaks are the main cause of energy waste in compressed air systems. Estimates show that up to 20% of total compressed air consumption may be lost through leaks. For this reason, reducing air leaks can be the single biggest energy saving measure you can take. Leaks near the compressor are usually the costliest due to the high-pressure environment. However, these leaks are thankfully rare. More common leaks occur at pipe joints, flanges, fittings, and condensation traps.
The most effective and reliable way to check for leaks is by using an ultrasonic acoustic detector. This type of detector picks up high-frequency noise waves that a leak makes. When a leak is present, the air no longer moves in the same direction and creates turbulent air inside pipes. An ultrasonic acoustic detector can interpret that noise and identify where the sound is coming from, even in very noisy environments.
If you don’t have one already, AirAudit’s formal leak management program will also help reduce costs and energy wastage. Involve production supervisors and operators, as well as your maintenance engineers, for best results identifying and repairing leaks.
The Financial Cost of Sustainability
Energy costs make up more than half of a compressors total cost of ownership. So, optimising air systems to use less energy can reduce both the production cost of compressed air and a company’s carbon footprint.
It is important to consider the composition of your compressed air system when calculating operating costs versus compressed air production rate. For example, poor piping design is often overlooked as a serious reason for pressure loss, despite certain layout options causing back pressure within the system. Ideally, there should be no pressure loss created by the piping system alone.
A common layout design in compressed air production is the installation of 90-degree tee connections. These connections create turbulence equal to 0.21 to 0.34 bar of pressure loss. Your system must work to make up for this added pressure, resulting in an extra PKR 90,000/- to PKR 150,000/- in energy expenses to maintain the desired system pressure.
While certain components of the production line may suggest a specific operating pressure, it does not mean that this is the pressure required for the entire compressed air system. For this reason, it is important to know what the pressure rating of each component is to avoid wasting compressed air wastage and increased energy exertion.
Maintain your system
Bad practice and poor maintenance can contribute to excess wastage. Continual monitoring and maintenance is key to a sustainable and efficient compressed air system. You should regularly service and performance test all of your compressed air equipment. This includes regularly replacing filters and making sure all components are clean. Correctly maintained filters can help guarantee air quality and help prevent pressure drop.
Our Partners at Sakoon Pneumatics offer yearly service contracts to take this burden out for you.