To improve the delivery of compressed air at the plant, the manufacturer took an important first step by using airflow meters to monitor and measure the performance of both systems. Subsequent planning based on actionable data led to a unique compressed air system upgrade that increases the plant’s ability to maintain peak production of high quality at all times.
This compressed air assessment was done on a system that had optimum components installed. The system had a four compressors, dryers, and large storage tank, yet still the system was running inefficiently because moisture and rust found in main line and huge volume of leakages. This problem was caused by inattention by both operators and the service provider to the proper way to operate these premium components.
AirAudit saved PKR 6.1 Million per year in energy costs, it is 17.72 % of energy of total energy consumption of that plant. The facility is one of the leading manufacturing organizations in Pakistan producing high quality transmission gears. The project payback is achieved in less than one year.
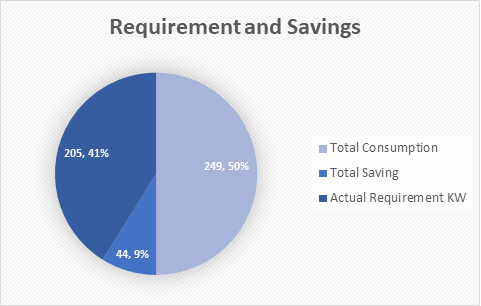
Approximate Losses by Area
Areas | Losses |
Dusty Environment: Service Kit | PKR 683,360.00 per annum |
Compressors’ Efficiency Evaluation | PKR 1,045,440.00 per annum |
Compressed Air Leakages | PKR 5,114,880.00 per annum |
Total Losses | PKR 6,843,680.00 per annum |

Conclusions and recommendations
We inspected and evaluated the concerned compressed air system in detail and have found it to be inefficient but with some attention, the company may save a significant amount in energy cost.
Compressors Room
Some inefficiencies were found in compressor room i.e. all compressors should be placed in a properly designed compressor room for their most efficient operation.
Dryers’ Performance:
Dryers was not working efficiently, temperature difference before and after dryer is less than was 5 degree Celsius, which is not good.
Air Distribution Network:
Piping network was observed and some sharp bends have been noticed, some piping supports are not proper, corroded piping at some places, mostly open ended. Ordinary GI/MS pipe has been used together with ordinary plumbing water GI/MS fittings at some areas, which are not recommended for compressed air.
Absence of pressure gauges on distribution piping. Pressure drops needs to be monitored and then eradicated.
We recommended them to install a new compressed air piping system (ideally aluminum), which is made and designed for compressed air and gas transmission, and not water. The fitting of such systems are totally different from those employed in normal low pressure water systems. These cater to the need for maintaining air flow, air pressure at all bends, junctions and connections, while being resistant to corrosion which occurs when GI/MS pipes carry moisture laden compressed air.
Leakages:
A high frequency of compressed air leakage has been found in production area especially in Grinding and Clamp Cell Department, which was detected carefully through our electronic audit equipment, which results in increased usage of electricity and un-necessary wear and tear on the compressors.
There is an opportunity of cost saving potential as discussed and evaluated earlier. The implementation of the recommendations mentioned above is the most essential part of the audit, we expect you to keep them on your highest priority and call us soon for the verification of it.
Contact AirAudit Compressed Air Consulting, a company specializing in compressed air efficiency consulting and training for more information and/or queries.